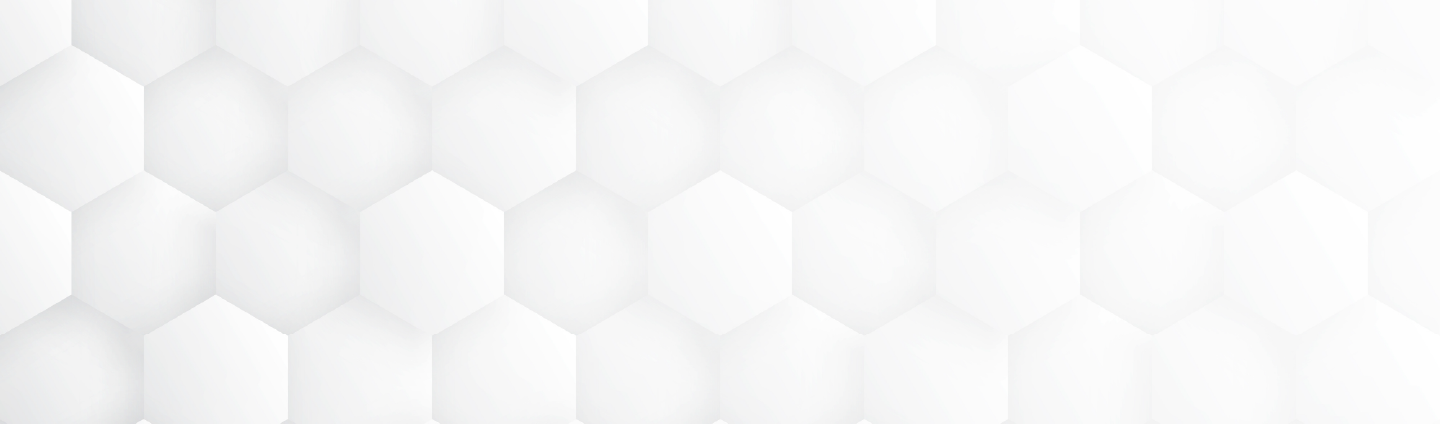
Featured Events
Enhance your composites journey & network at ACMA events.
Media Kit
Reach top composites leaders with targeted print/digital ads.
CGI Committees
Join our committees and use your expertise to drive change.
Certification
Pursue certifications that will enhance your skills and career.
ACMA ON THE MOVE
August 22, 2025
August 20, 2025
August 20, 2025
August 20, 2025
August 20, 2025
August 20, 2025
Keep me Informed
Subscribe now for ACMA updates and industry news. Stay informed and connected with the composites industry. Join us today for the latest insights!
SubscribeRead Latest Edition
Dive into compelling industry stories, insights, and visuals. Explore now for an enriching experience. Don’t miss out – read it today.
Learn More